Kako se obrađuju visoko precizni dijelovi
2023-09-22
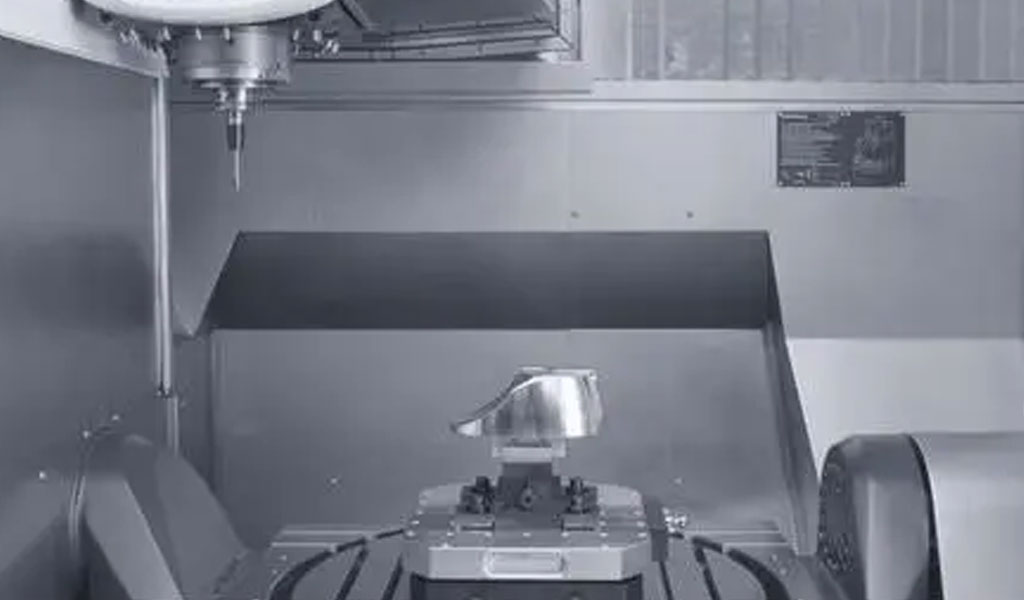
Razumijevanje precizne obrade
Precizna obrada je kamen temeljac moderne proizvodnje, odgovoran za proizvodnju složenih i preciznih komponenti koje se koriste u širokom spektru industrija. Da bismo u potpunosti shvatili njen značaj, hajde da istražimo osnovne koncepte precizne obrade, njenu vitalnu ulogu u različitim sektorima i istorijski put koji je doveo do njenog trenutnog stanja izvrsnosti.A. Šta je precizna obrada?
Precizna obrada se odnosi na skup proizvodnih procesa koji uklanjaju materijal sa radnog komada sa visokim stepenom tačnosti i kontrole, što rezultira fino izrađenim komponentama sa malim tolerancijama. Ovaj proces pretvara sirovine, kao što su metali, plastika ili keramika, u precizne dijelove koji ispunjavaju precizne specifikacije. Ključne karakteristike precizne obrade uključuju:- preciznost: Precizna obrada osigurava da se finalni proizvod precizno prilagodi predviđenom dizajnu, uz minimalna odstupanja.
- Tight Tolerances: Omogućava proizvodnju dijelova s ekstremno malim tolerancijama, što znači da se gotove komponente usko pridržavaju specificiranih mjera.
- Superiorna završna obrada: Precizna obrada pruža izuzetnu završnu obradu površine, često eliminirajući potrebu za dodatnim procesima završne obrade.
- Kompleksne geometrije: Može stvoriti zamršene oblike, konture i karakteristike, što ga čini nezamjenjivim u proizvodnji komponenti sa složenim dizajnom.
- Ponovljivost: Preciznost proces mašinske obradeovi su vrlo ponovljivi, osiguravajući dosljedan kvalitet u više dijelova.
- prilagodljivost: Može se primijeniti na širok spektar materijala, što ga čini pogodnim za različite industrije.
B. Važnost precizne obrade
Precizna obrada ima ogroman značaj u nekoliko kritičnih industrija, utičući na različite aspekte našeg svakodnevnog života. Evo nekoliko uvjerljivih razloga za njegovu važnost:- Vazduhoplovstvo: U sektoru vazduhoplovstva, precizna obrada je neophodna za izradu komponenti koje izdržavaju ekstremne uslove. Motori aviona, sletanje zupčanik, a strukturni elementi se oslanjaju na precizno obrađene dijelove za sigurnost i performanse.
- medicinski uređaji: Medicinski uređaji poput hirurških instrumenata, protetika i implantabilnih uređaja zahtijevaju preciznu mašinsku obradu radi biokompatibilnosti, tačnosti i sigurnosti pacijenata.
- Automotive Sector: Precizno obrađeni dijelovi su neophodni za automobilsku industriju kako bi se osigurala pouzdanost i efikasnost vozila. Komponente kao što su dijelovi motora, sistemi prijenosa i kočioni mehanizmi oslanjaju se na preciznu mašinsku obradu.
- Elektronika i poluvodiči: Precizna obrada je ključna u proizvodnji mikroelektronskih komponenti i poluvodičkih uređaja, gdje su minimalne tolerancije imperativ za funkcionalnost.
- Energetski sektor: Energetska industrija se oslanja na preciznu mašinsku obradu za proizvodnju kritičnih delova koji se koriste u proizvodnji električne energije, uključujući turbine, generatore i komponente prenosa.
- Izrada alata i kalupa: Precizna obrada je ključna u proizvodnji alata i kalupa, koji se, pak, koriste za stvaranje bezbroj drugih proizvoda.
- Consumer Electronics: Proizvodnja pametnih telefona, laptopa i druge potrošačke elektronike ima koristi od precizne obrade kako bi se osigurao elegantan dizajn i optimalna funkcionalnost.
- Istraživanje i razvoj: Istraživači i naučnici ovise o precizno obrađenim komponentama za eksperimente, prototipove i laboratorijsku opremu.
C. Istorijska perspektiva
Putovanje precizne mašinske obrade seže do drevnih civilizacija, gde su vešti zanatlije koristili rudimentarne alate za oblikovanje materijala. Međutim, preciznost postignuta u to vreme bila je ograničena u poređenju sa savremenim standardima.- Rana precizna obrada: Industrijska revolucija 18. i 19. stoljeća označila je ključni period u razvoju precizne strojne obrade. Izum alatnih mašina, kao što su strugovi i glodalice, revolucionirao je proizvodnju omogućavajući veću tačnost i konzistentnost.
- Drugi svjetski rat: Precizna obrada imala je ključnu ulogu u Drugom svjetskom ratu, jer je bila neophodna za proizvodnju vojne opreme sa potrebnom preciznošću i uniformnošću. Ovo doba je svjedočilo napretku u tehnikama strojne obrade i pojavi novih materijala.
- Poslijeratni napredak: U poslijeratnom periodu došlo je do porasta tehnoloških inovacija, uključujući upotrebu kompjuterskih mašina za numeričko upravljanje (CNC). CNC obrada omogućava automatizovane i visoko precizne operacije, otvarajući novu eru proizvodnje.
- Digitalno doba: Integracija računara i softvera u procese obrade dodatno je podigla preciznu mašinsku obradu. Moderne CNC mašine mogu izvršavati složene operacije sa neuporedivom preciznošću, što ih čini nezamjenjivim u današnjem proizvodnom okruženju.
Materijali i njihov značaj
Materijali su temelj precizne obrade, a odabir pravog materijala igra ključnu ulogu u proizvodnji visoko preciznih dijelova. U ovom odeljku ćemo se pozabaviti značajem odabira odgovarajućih materijala, razumeti značaj svojstava materijala i istražiti različite faktore koji utiču na obradivost.A. Izbor materijala
Izbor materijala u preciznoj mašinskoj obradi je kritična odluka koja direktno utiče na performanse, trajnost i funkcionalnost konačnog proizvoda. Proizvođači moraju uzeti u obzir nekoliko faktora pri odabiru materijala:- Pogodnost materijala: Materijal mora biti prikladan za predviđenu primjenu. Različite industrije i primjene imaju različite zahtjeve, kao što su otpornost na temperaturu, otpornost na koroziju i električnu provodljivost.
- mehaničke osobine: Mehanička svojstva poput vlačne čvrstoće, tvrdoće i duktilnosti su presudna. Na primjer, u vazduhoplovstvu, materijali visoke vlačne čvrstoće su poželjniji za strukturne komponente.
- Toplinska svojstva: Za neke primene su potrebni materijali sa odličnom toplotnom provodljivošću ili otpornošću na visoke temperature. Ovo je posebno važno u industrijama kao što su proizvodnja električne energije i elektronika.
- Otpor koroziji: U okruženjima u kojima je korozija zabrinjavajuća, poželjni su materijali sa visokom otpornošću na koroziju, kao što su nerđajući čelik ili titanijum.
- Razmatranje težine: Industrije poput automobilske i svemirske industrije često daju prednost lakim materijalima kao što su aluminij ili kompoziti od karbonskih vlakana kako bi se smanjila potrošnja goriva i poboljšale performanse.
- Cost Constraints: Trošak je značajan faktor u odabiru materijala. Materijali visokih performansi mogu biti skupi, tako da proizvođači moraju uspostaviti ravnotežu između performansi i isplativosti.
- Usklađenost sa propisima: U industrijama kao što je zdravstvo, materijali moraju ispunjavati stroge regulatorne standarde za biokompatibilnost i sigurnost.
- dostupnost: Dostupnost materijala i njihovi izvori također utiču na odabir. Neke specijalizirane legure ili kompoziti mogu imati ograničenu dostupnost.
B. Svojstva materijala
Razumijevanje svojstava materijala je ključno za preciznu obradu. Evo nekih ključnih svojstava materijala i njihovog značaja:- Zatezna čvrstoća: Vlačna čvrstoća mjeri sposobnost materijala da izdrži silu vuče bez loma. Neophodan je za strukturne komponente i dijelove koji su podvrgnuti mehaničkom naprezanju.
- tvrdoća: Tvrdoća označava otpornost materijala na deformaciju i habanje. Tvrdi materijali su pogodni za rezne alate, dok se mekši materijali mogu preferirati za određene primjene, poput brtvi.
- Duktilnost: Duktilnost se odnosi na sposobnost materijala da se deformira bez loma kada je podvrgnut vlačnom naprezanju. Duktilni materijali se lakše oblikuju, ali možda nisu prikladni za aplikacije koje zahtijevaju krutost.
- Toplotna provodljivost: Materijali visoke toplotne provodljivosti efikasno odvode toplotu. Ovo svojstvo je od vitalnog značaja u aplikacijama gde je kontrola temperature kritična.
- Električna provodljivost: Električna provodljivost je neophodna u elektronici i električnim komponentama, gdje materijali moraju olakšati protok električne energije.
- Magnetska svojstva: Magnetna svojstva su značajna u industrijama kao što su elektromagnetika i elektronika, gdje materijali moraju biti feromagnetni ili nemagnetni.
- Hemijski otpor: Materijali moraju biti otporni na hemijsku koroziju u sredinama gdje su izloženi kiselinama, bazama ili drugim korozivnim supstancama.
C. Faktori obradivosti
Obradivost se odnosi na lakoću s kojom se materijal može obraditi, rezati ili oblikovati. Na njega utiču različiti faktori, uključujući:- Tvrdoća materijala: Mekši materijali se generalno lakše obrađuju, dok tvrđi materijali mogu zahtijevati specijalizirane alate i tehnike.
- Formiranje čipova: Formiranje i evakuacija strugotine tokom obrade utiče na efikasnost procesa i završnu obradu površine.
- Tool Wear: Različiti materijali mogu uzrokovati različite stepene habanja alata, utičući na brzinu obrade i troškove.
- Rashladna tečnost i podmazivanje: Pravilno rashladno sredstvo i podmazivanje su neophodni za smanjenje trenja, toplote i habanja alata tokom obrade.
- Brzina sečenja: Brzina kojom se rezni alat kreće kroz materijal utiče i na produktivnost i na kvalitet obrađene površine.
- Materijal alata: Izbor materijala reznog alata, kao što je karbid ili brzorezni čelik, ovisi o materijalu koji se obrađuje.
- Parametri rezanja: Podešavanje parametara rezanja kao što su brzina pomaka i dubina rezanja može optimizirati proces obrade za određene materijale.
Mašinski alati za preciznu obradu
Alatne mašine su srce precizne mašinske obrade, omogućavajući transformaciju sirovina u visoko precizne delove. U ovom odeljku ćemo istražiti četiri ključne vrste mašina alatki koje se koriste u preciznoj mašinskoj obradi: CNC obradni centri, mašine za struganje, mašine za brušenje i EDM (električna obrada). Svaka od ovih mašina igra jedinstvenu ulogu u proizvodnji preciznih komponenti.A. CNC obradni centri
CNC (kompjuterska numerička kontrola) obradni centri su svestrani i široko se koriste u preciznoj obradi. Oni su automatizovani sistemi koji kontrolišu kretanje reznih alata i radnih komada sa izuzetnom preciznošću. Evo pregleda CNC obradnih centara i njihovog značaja:- prilagodljivost: CNC obradni centri mogu izvoditi različite operacije obrade, uključujući glodanje, bušenje i urezivanje. Ova svestranost omogućava proizvodnju složenih delova sa više funkcija.
- Visoka preciznost: Kompjuterizirana kontrola CNC mašina osigurava precizno pozicioniranje alata i konzistentne rezultate, što ih čini idealnim za dijelove sa malim tolerancijama.
- automatizacija: CNC obradni centri mogu raditi kontinuirano, uz minimalnu ljudsku intervenciju. Ova automatizacija povećava efikasnost i smanjuje rizik od grešaka.
- Kompleksne geometrije: Ističu u obradi zamršenih oblika i kontura, što ih čini pogodnim za industrije kao što je svemir, gdje su složene komponente uobičajene.
- Ponovljivi rezultati: CNC mašine nude odličnu ponovljivost, osiguravajući da svaki proizvedeni dio odgovara tačnim specifikacijama dizajna.
- Smanjeno vrijeme postavljanja: CNC obradni centri mogu se programirati da brzo prelaze između različitih zadataka, minimizirajući vrijeme postavljanja i povećavajući efikasnost proizvodnje.
B. Strojevi za struganje
Strojevi za struganje se koriste za stvaranje cilindričnih dijelova rotacijom radnog komada dok rezni alat uklanja materijal sa njegove vanjske površine. Oni su neophodni za proizvodnju vratilos, igle i druge komponente sa rotacijskom simetrijom. Ključne tačke o mašinama za struganje uključuju:- Cilindrični dijelovi: Strojevi za struganje specijalizirani su za proizvodnju cilindričnih ili cijevnih komponenti, uključujući one s navojima ili zamršenim žljebovima.
- Visoke brzine: Rade pri velikim brzinama, što ih čini pogodnim za dijelove koji zahtijevaju glatku i preciznu završnu obradu.
- Jednoosni rad: Većina strojeva za struganje su jednoosni, fokusirajući se na oblikovanje vanjske površine radnog komada.
- Efikasan za masovnu proizvodnju: Tokarenje je veoma efikasno za delove masovne proizvodnje sa minimalnim otpadom materijala.
- Lathe Machines: Ručne i CNC kontrolisane tokarilice su obično korišćene mašine za struganje, nudeći niz mogućnosti.
C. Mašine za mlevenje
Mašine za brušenje su dizajnirane za preciznu završnu obradu i oblikovanje tvrdih ili abrazivnih materijala. Oni su ključni za postizanje izuzetno čvrstih tolerancija i vrhunske završne obrade. Evo zašto su mašine za mlevenje važne:- Preciznost na mikronskom nivou: Mašine za mljevenje mogu postići preciznost na nivou mikrona, što ih čini neophodnim za aplikacije koje zahtijevaju najviši nivo tačnosti.
- Uklanjanje materijala: Uklanjaju materijal abrazijom, omogućavajući korekciju nesavršenosti površine i postizanje izuzetne glatkoće.
- Brušenje alata i rezača: Pored površinskog brušenja, postoje specijalizovane mašine za brušenje za oštrenje reznih alata i izradu preciznih profila.
- Raznolikost metoda brušenja: Različite vrste mašina za brušenje, uključujući površinske brusilice, cilindrične brusilice i brusilice bez centra, zadovoljavaju različite potrebe obrade.
- Hardened Materials: Brušenje je posebno pogodno za kaljene materijale poput alatnog čelika i keramike, gdje tradicionalne metode obrade mogu biti neučinkovite.
D. EDM (električna obrada)
EDM, ili obrada električnim pražnjenjem, je netradicionalni proces obrade koji koristi električna pražnjenja za oblikovanje materijala. Idealan je za stvaranje zamršenih i osjetljivih dijelova gdje tradicionalni alati za rezanje mogu uzrokovati štetu. Ključni aspekti EDM-a uključuju:- Nema fizičkog kontakta: EDM ne uključuje direktan fizički kontakt između alata i radnog komada, minimizirajući rizik od habanja alata i oštećenja lomljivih materijala.
- Visoka preciznost: Može postići visoku preciznost i kvalitet završne obrade, čak i sa izuzetno tvrdim materijalima.
- Wire EDM i Sinker EDM: Postoje dvije osnovne vrste EDM mašina: rezanje žice EDM, koji koristi žičanu elektrodu, i sinker EDM, koji koristi oblikovanu elektrodu.
- Complex Shapes: EDM može proizvesti složene oblike, kao što su kalupi i kalupi, sa zamršenim detaljima i finim karakteristikama.
- Toplotno pogođena zona: Budući da EDM ne stvara toplinu na radnom komadu, pogodan je za materijale osjetljive na toplinu kao što su legure za zrakoplovstvo.
- Sporo proces: EDM je relativno spor u poređenju sa drugim metodama obrade, što ga čini najprikladnijim za male količine, visoko precizne poslove.
Alati za rezanje i alat
Alati za rezanje su na čelu precizne obrade, služe kao instrumenti koji oblikuju i pretvaraju sirovine u visoko precizne dijelove. U ovom dijelu ćemo istražiti različite vrste reznih alata, važnost premaza alata i faktore koji utječu na vijek trajanja i habanje alata.A. Vrste reznih alata
Precizna obrada oslanja se na raznoliku paletu reznih alata, od kojih je svaki dizajniran za specifične zadatke i materijale. Izbor alata za sečenje u velikoj meri utiče na efikasnost i tačnost procesa obrade. Evo nekoliko uobičajenih vrsta alata za rezanje:- End Mills: Završne glodalice su svestrani alati koji se koriste za operacije glodanja. Imaju više reznih rubova i mogu ukloniti materijal sa radnog komada na različite načine, uključujući oblaganje, konturiranje i urezivanje.
- Bušilice: Bušilice su dizajnirane za stvaranje rupa u radnim komadima. Dolaze u različitim oblicima, uključujući spiralne bušilice, centralne bušilice i bušilice koje se mogu indeksirati.
- Turning Inserts: Koriste se u mašinama za struganje za oblikovanje cilindričnih dijelova. Umetci za okretanje dostupni su u različitim oblicima i materijalima koji odgovaraju različitim primjenama.
- Milling Cutters: Glodalice dolaze u različitim oblicima, kao što su čeoni glodali, kuglični mlinovi i glodalice za urezivanje, a koriste se u mašinama za glodanje za kreiranje različitih karakteristika na radnom komadu.
- Razvrtači: Razvrtači se koriste za završnu obradu i dimenzioniranje prethodno izbušenih rupa do preciznih dimenzija. Oni osiguravaju glatke i precizne površine rupa.
- Taps and Dies: Ovi alati za sečenje se koriste za operacije narezivanja navoja. Slavine stvaraju unutrašnje navoje, dok matrice stvaraju vanjske navoje.
- Brusni točkići: Brusni točkovi su abrazivni alati koji se koriste za precizno brušenje površine. Dostupni su u različitim abrazivnim materijalima i veličinama zrna.
- Broaches: Broševi su specijalizirani alati koji se koriste za rezanje unutrašnjih i vanjskih oblika i profila, kao što su žljebovi i klinovi.
- Protoci i upuštači: Ovi alati se koriste za pravljenje udubljenja ili ivica oko rupa za pričvršćivačs.
- Boring Bars: Šipke za bušenje se koriste u operacijama bušenja za povećanje postojećih rupa s preciznošću.
B. Premazi alata
Premazi alata su tanki slojevi materijala koji se nanose na rezne alate kako bi se poboljšale njihove performanse i izdržljivost. Ovi premazi nude nekoliko prednosti:- Reduced Friction: Premazi poput titanijum nitrida (TiN) i titan karbonitrida (TiCN) smanjuju trenje između alata i obratka, što dovodi do glatkog rezanja i dužeg vijeka trajanja alata.
- Povećana tvrdoća: Premazi povećavaju tvrdoću površine alata, čineći ga otpornijim na habanje i produžavajući vijek trajanja alata.
- Poboljšana otpornost na toplotu: Premazi mogu izdržati visoke temperature koje nastaju tokom obrade, smanjujući trošenje alata uzrokovano toplinom i povećavajući brzinu rezanja.
- Svojstva protiv nakupljanja: Neki premazi imaju svojstva protiv prianjanja, sprečavajući nakupljanje materijala na reznim rubovima alata.
- Povećana mazivost: Alati sa premazom imaju poboljšanu sposobnost podmazivanja, smanjujući potrebu za prekomjernom rashladnom tečnošću i poboljšavajući evakuaciju strugotine.
C. Vijek trajanja i habanje alata
Razumijevanje vijeka trajanja alata i habanja je ključno za optimizaciju procesa obrade i minimiziranje troškova proizvodnje. Vijek trajanja alata odnosi se na vrijeme dok rezni alat ostaje efikasan prije nego što zahtijeva zamjenu ili popravku. Nekoliko faktora utiče na vijek trajanja i habanje alata:- Brzina sečenja: Veće brzine rezanja mogu dovesti do povećanog trošenja alata zbog viših temperatura koje nastaju tokom obrade. Pravilan odabir brzina rezanja je bitan za balansiranje vijeka trajanja alata i produktivnosti.
- Feed Rate: Brzina kojom rezni alat napreduje u radni komad utječe na trošenje alata. Visoke brzine pomaka mogu ubrzati habanje, dok niže brzine pomaka mogu produžiti vijek trajanja alata.
- Dubina reza: Dubina reza utječe na količinu uklonjenog materijala po prolazu. Dublji rezovi mogu povećati trošenje alata, tako da je optimizacija dubine kritična.
- Tvrdoća materijala: Rezanje tvrdih materijala može ubrzati habanje alata. Za efikasnu obradu tvrdih materijala koriste se specijalni alati i premazi.
- Rashladna tečnost i podmazivanje: Odgovarajuće sredstvo za hlađenje i podmazivanje pomažu u rasipanju topline i smanjenju trenja, produžavajući vijek trajanja alata.
- Materijal alata: Materijal od kojeg je napravljen rezni alat utiče na njegovu otpornost na habanje. Materijali poput karbida i keramike nude odličnu otpornost na habanje.
- Geometrija alata: Geometrija alata za sečenje, uključujući nagibni ugao, ugao reljefa i dizajn lomača strugotine, igra značajnu ulogu u obrascima habanja.
- Materijal radnog komada: Vrsta materijala koji se obrađuje utiče na habanje alata. Abrazivni materijali mogu dovesti do bržeg trošenja alata.
Precizni procesi obrade
Precizni procesi strojne obrade su metode kojima se sirovine pretvaraju u visoko precizne dijelove sa malim tolerancijama i izvanrednom završnom obradom površine. U ovom odeljku ćemo istražiti pet ključnih preciznih procesa obrade: tokarenje, glodanje, bušenje, brušenje i obrada sa električnim pražnjenjem (EDM). Svaki od ovih procesa služi jedinstvenoj svrsi i koristi se na osnovu specifičnih zahtjeva radnog komada.A. Okretanje
Tokarenje je proces obrade koji se prvenstveno koristi za oblikovanje cilindričnih dijelova. Uključuje rotaciju radnog komada dok alat za rezanje u jednoj tački uklanja materijal sa vanjske površine. Evo ključnih aspekata okretanja:- Cilindrični dijelovi: Tokarenje je idealno za proizvodnju cilindričnih komponenti kao što su osovine, klinovi i čahure.
- Rotaciona simetrija: Pogodan je za dijelove koji zahtijevaju simetriju rotacije, jer se radni komad rotira na strugu dok ga rezni alat oblikuje.
- Razne operacije: Tokarenje može obavljati različite operacije, uključujući oblaganje, okretanje (smanjenje prečnika), konusno okretanje i urezivanje navoja.
- Sečenje u jednoj tački: Jedan alat za rezanje uklanja materijal u kontinuiranom kretanju, što rezultira efikasnim uklanjanjem materijala.
- Lathe Machines: I ručni i CNC upravljani strugovi se obično koriste za operacije tokarenja.
B. Glodanje
Glodanje je svestran precizan proces obrade koji koristi alate za rezanje u više tačaka za uklanjanje materijala sa radnog komada. Pogodan je za stvaranje širokog spektra oblika i karakteristika. Ključni aspekti mljevenja uključuju:- prilagodljivost: Glodanje može proizvesti ravne površine, utore, džepove i složene konture. Koristi se i za 2D i 3D obradu.
- Rezanje u više tačaka: Više reznih ivica na alatu istovremeno komunicira sa radnim predmetom, omogućavajući efikasno uklanjanje materijala.
- Vrste glodanja: Glodanje se može izvoditi pomoću različitih vrsta glodala, uključujući krajnje glodalice, čeone glodalice i kuglaste glodalice.
- CNC obradni centri: CNC upravljane glodalice nude preciznu kontrolu kretanja alata i naširoko se koriste u modernoj mašinskoj obradi.
- Visoke brzine: Glodanje se može izvoditi pri velikim brzinama, što omogućava efikasnu proizvodnju.
C. Bušenje
Bušenje je precizan proces obrade koji se koristi za stvaranje rupa u radnim komadima. To je osnovna operacija u raznim industrijama. Ključni aspekti bušenja uključuju:- Kreiranje rupa: Mašine za bušenje koriste specijalizovane alate zvane bušilice za uklanjanje materijala i stvaranje rupa određenih prečnika.
- Vrste bušilica: Dostupne su različite vrste bušilica, uključujući spiralne bušilice, centralne bušilice i bušilice koje se mogu indeksirati, svaka dizajnirana za specifične primjene.
- preciznost: Precizno pozicioniranje i poravnavanje su neophodni u bušenju kako bi se osiguralo da se rupe prave s preciznošću.
- Brzina i brzina uvlačenja: Parametri bušenja kao što su brzina rotacije i brzina pomaka su kritični za postizanje željenih dimenzija rupe.
- Rashladna tečnost i podmazivanje: Odgovarajuća tečnost za hlađenje i podmazivanje se koriste za odvođenje toplote i smanjenje trenja tokom bušenja.
D. Brušenje
Brušenje je precizan proces obrade koji koristi abrazivne točkove za uklanjanje materijala i postizanje izuzetno čvrstih tolerancija i završne obrade površine. Ključni aspekti mljevenja uključuju:- Izuzetna preciznost: Brušenje može postići preciznost na nivou mikrona, što ga čini idealnim za aplikacije koje zahtijevaju najveću preciznost.
- Završno: Proizvodi vrhunske završne obrade površine, često eliminirajući potrebu za dodatnim procesima završne obrade.
- Materijali: Brušenje je pogodno za tvrde i abrazivne materijale, uključujući kaljeni čelik, keramiku i karbide.
- Raznolikost metoda brušenja: Različite vrste mašina za brušenje, kao što su površinske brusilice, cilindrične brusilice i brusilice bez centra, zadovoljavaju različite potrebe obrade.
- Rashladno sredstvo: Pravilna rashladna tečnost je neophodna za brušenje kako bi se spriječilo pregrijavanje i održao integritet kotača.
E. Obrada električnim pražnjenjem (EDM)
EDM, ili obrada električnim pražnjenjem, je netradicionalni precizan proces obrade koji koristi električna pražnjenja za uklanjanje materijala. Posebno je prikladan za obradu složenih i zamršenih oblika, kao i tvrdih materijala otpornih na toplinu. Ključni aspekti EDM-a uključuju:- Beskontaktna obrada: EDM ne uključuje direktan kontakt između alata i radnog komada, smanjujući rizik od habanja i oštećenja alata.
- Visoka preciznost: EDM može postići visoku preciznost, što ga čini pogodnim za primjene gdje su čvrste tolerancije bitne.
- Complex Shapes: Odlikuje se u obradi složenih oblika, kalupa, kalupa i komponenti sa finim detaljima.
- Wire EDM i Sinker EDM: Postoje dva primarna tipa EDM mašina: žičana EDM, koja koristi žičanu elektrodu, i EDM sa potopom, koja koristi oblikovanu elektrodu.
- Sporo proces: EDM je relativno spor u poređenju sa drugim metodama obrade, što ga čini najprikladnijim za male količine, visoko precizne poslove.
Tolerancije i kontrola kvaliteta
Precizna obrada zahtijeva pažljivu pažnju na detalje i rigoroznu posvećenost kontroli kvaliteta kako bi se osiguralo da dijelovi ispunjavaju specificirane standarde. U ovom odeljku ćemo istražiti tri kritična aspekta kontrole kvaliteta u preciznoj mašinskoj obradi: geometrijsko dimenzionisanje i toleranciju (GD&T), statističku kontrolu procesa (SPC) i osiguranje kvaliteta.A. Geometrijsko dimenzioniranje i tolerancija (GD&T)
Geometrijsko dimenzionisanje i tolerancija, često skraćeno GD&T, je sistem koji se koristi za definisanje i saopštavanje dozvoljenih varijacija u veličini, obliku, orijentaciji i lokaciji karakteristika na delu. GD&T je od vitalnog značaja u preciznoj mašinskoj obradi iz sledećih razloga:- Precise Communication: GD&T pruža standardizirani jezik za inženjere, dizajnere i mašiniste da precizno prenesu namjeru dizajna i zahtjeve dimenzija.
- Pojašnjenje tolerancije: Pomaže u definiranju prihvatljivih varijacija u kritičnim dimenzijama, osiguravajući da svi dionici razumiju dozvoljena odstupanja.
- Poboljšan kvalitet: GD&T promoviše poboljšani kvalitet smanjujući dvosmislenost u specifikacijama dizajna, minimizirajući rizik od grešaka tokom obrade.
- Efikasnost troškova: Jasne GD&T specifikacije mogu dovesti do smanjenih troškova proizvodnje, jer je manja vjerovatnoća da će dijelovi biti rashodovani ili zahtijevati doradu zbog nesporazuma ili pogrešnog tumačenja.
- Complex Geometry: Posebno je koristan za dijelove složene geometrije, osiguravajući da su sve karakteristike proizvedene prema željenim specifikacijama.
B. Statistička kontrola procesa (SPC)
Statistička kontrola procesa (SPC) je metodologija kontrole kvaliteta koja koristi statističke tehnike za praćenje i kontrolu procesa obrade. SPC je neophodan u preciznoj mašinskoj obradi iz sledećih razloga:- Nadgledanje procesa: SPC pomaže u praćenju procesa obrade u realnom vremenu, identifikujući varijacije ili odstupanja od željenih parametara.
- Rano otkrivanje problema: Kontinuiranim praćenjem procesa, SPC omogućava rano otkrivanje problema koji bi mogli dovesti do dijelova izvan specifikacije, smanjenja otpada i prerade.
- Donošenje odluka vođeno podacima: SPC se oslanja na podatke i statističku analizu za donošenje informiranih odluka o prilagođavanju procesa, osiguravajući da proces obrade ostane u prihvatljivim granicama.
- Poboljšana konzistentnost: SPC promovira konzistentnost procesa i smanjuje vjerovatnoću proizvodnje neusklađenih dijelova.
- Smanjeni otpad i prerada: Prompnim identifikovanjem i adresiranjem varijacija procesa, SPC minimizira proizvodnju neispravnih delova, smanjujući troškove otpada i prerade.
C. Osiguranje kvaliteta u preciznoj obradi
Osiguranje kvaliteta u preciznoj mašinskoj obradi obuhvata sveobuhvatan pristup osiguravanju da proizvedeni dijelovi ispunjavaju ili premašuju specificirane standarde kvaliteta. Uključuje različite elemente, uključujući:- Procesna dokumentacija: Detaljna dokumentacija procesa obrade, uključujući standardne radne procedure (SOP) i radne upute, osigurava da se svaki korak izvodi dosljedno.
- Inspekcija i mjerenje: Rigorozna inspekcija i merenje korišćenjem preciznih instrumenata i metroloških tehnika potvrđuje da su delovi usklađeni sa određenim tolerancijama i standardima kvaliteta.
- kalibrisanje: Redovna kalibracija opreme za mašinsku obradu i mernih instrumenata je neophodna za održavanje tačnosti i sledljivosti.
- Verifikacija materijala: Provjera svojstava materijala, sastava i kvaliteta je kritična kako bi se osiguralo da korišteni materijal ispunjava zahtjeve dizajna.
- Obuka zaposlenih: Programi obuke i razvoja vještina za mašiniste i osoblje za kontrolu kvaliteta osiguravaju da oni budu stručni u svojim ulogama i odgovornostima.
- Analiza osnovnog uzroka: Kada se identifikuju neusaglašeni delovi, sprovodi se analiza osnovnog uzroka kako bi se utvrdio izvor problema i sprovele korektivne mere.
- Kontinuirano poboljšanje: Kultura stalnog poboljšanja podstiče inovacije i pokreće stalna poboljšanja u procesima obrade i postupcima kontrole kvaliteta.
- Customer Feedback: Prikupljanje i analiza povratnih informacija kupaca pomaže u identifikaciji područja za poboljšanje i usklađuje procese obrade sa očekivanjima kupaca.
zaključak
A. Umjetnost i nauka precizne obrade
Precizna obrada je na raskrsnici umjetnosti i nauke, gdje se kreativnost, vještina i inovacija spajaju kako bi proizveli visoko precizne dijelove koji pokreću industrije i oblikuju moderni svijet. To je i umjetnička forma, koja zahtijeva zanatsko umijeće i stručnost mašinista koji pretvaraju sirovine u radove inženjerske izvrsnosti, i znanost koja se oslanja na najsavremeniju tehnologiju, nauku o materijalima i napredne procese kako bi se postigla neuporediva preciznost. Putovanje precizne strojne obrade vodi nas kroz razumijevanje materijala i njihovih svojstava, ovladavanje alatima za rezanje i strojevima, te preciznu kontrolu procesa i tolerancija. Obuhvaća jezik geometrijskog dimenzioniranja i tolerancije, budnost statističke kontrole procesa i posvećenost osiguranju kvaliteta. Precizna obrada igra ključnu ulogu u različitim industrijama, od svemirske i automobilske do medicinskih uređaja i elektronike, oblikujući sve, od motora aviona do umjetnih zglobova i mikročipova. Omogućava stvaranje komponenti koje rade sa neusporedivom preciznošću i pouzdanošću, često pomerajući granice mogućeg.B. Završne misli
Kako zaključujemo ovo istraživanje precizne obrade, jasno je da se ovo polje ne bavi samo stvaranjem dijelova; radi se o stvaranju mogućnosti. Potraga za preciznošću pokreće inovacije, pomičući granice onoga što se može postići. Bilo da se radi o delikatnoj izradi koja je potrebna za stvaranje zamršenih zupčanika sata ili o naprednoj tehnologiji potrebnoj za proizvodnju složenih vazduhoplovnih komponenti, precizna obrada je u srcu svega. Budućnost precizne mašinske obrade puna je obećanja. Napredak u nauci o materijalima, automatizaciji i digitalnim tehnologijama nastavlja da preoblikuje krajolik. Minijaturizacija, 3D štampanje i održive proizvodne prakse postaju sve istaknutije, otvarajući nove horizonte za industriju. U svijetu u kojem je preciznost važnija nego ikad, precizna obrada ostaje nezamjenjiv stub modernog inženjerstva. To je dokaz ljudske genijalnosti i naše nepopustljive težnje za izvrsnošću u svakom aspektu proizvodnje. Kako potražnja za višom preciznošću i složenijim komponentama raste, precizna obrada će nastaviti da se razvija, suočavajući se s izazovima sutrašnjice sa istom posvećenošću i preciznošću koja je definirala vekovima.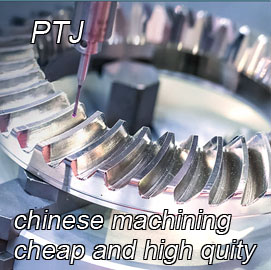
Naše usluge
- 5 osna obrada
- CNC glodanje
- Cnc okreće
- Strojna industrija
- Proces obrade
- Obrada površina
- Strojna obrada metala
- Obrada plastike
- Kalup za metalurgiju praha
- Die Casting
- Galerija delova
studije slučaja
- Auto metalni dijelovi
- Dijelovi mašina
- LED hladnjak
- Građevinski dijelovi
- Mobilni dijelovi
- Medicinski dijelovi
- Elektronički dijelovi
- Prilagođena obrada
- Delovi za bicikle
Popis materijala
- Obrada aluminijuma
- Obrada titana
- Obrada od nehrđajućeg čelika
- Mašinska obrada bakra
- Obrada mesinga
- Mašinska obrada super legura
- Peek Machining
- UHMW obrada
- Unilate Machining
- PA6 Strojna obrada
- PPS mašinska obrada
- Teflonska obrada
- Inconel Machining
- Mašinska obrada alata
- Više materijala
Galerija delova